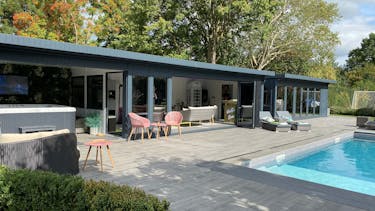
A housing development plagued with shrinking floors after construction has been saved by SMARTPLY SURE STEP, from MEDITE SMARTPLY.
The large new development on Kirvin Hill, Wicklow, Ireland is currently being built in three phases, and comprises approximately 50 – 100 homes per phase. Shortly after the completion of phase one, developer Broomhall Estates began receiving reports of gaps appearing between the floors and skirting boards in many of the new homes.
This was due to a combination of factors, but mainly the climate during the installation of the flooring system. The original product specified was proving to be unsuitable as, before the homes were sealed and completed, they proved prone to absorbing atmospheric moisture, which caused expansion. Once each house was completed, the interior atmosphere became much dryer, which allowed the boards to dry and shrink, causing significant gaps to form around the edges.
Part way through Phase 2 construction, subcontractor Derek Bradshaw of Bradshaw Carpentry, who was tasked with rectifying the issue, asked materials supplier Chadwicks to recommend an alternative product that could be used instead of the original specification for the remainder of the project.
Jason McMullan, Technical Sales Manager for MEDITE SMARTPLY explained: “I was called by the Chadwicks’ Bray branch in October 2021 with a request to recommend a product alternative to mitigate the risk of shrinkage. Resolving this was coming at a very high cost, and furthermore, the issue had only manifested well down the line after new owners had taken up occupancy. Not a good look.
“At the time, SMARTPLY SURE STEP had not yet been launched, but I knew it was going to be ideal for the job,” he said.
Manufactured in accordance with EN 300, SMARTPLY SURE STEP is a coated load bearing, tongue and groove OSB/3 panel, ideal for use as flooring or roof decking, where improved durability, reduced edge swelling, or reduced surface degradation are required on projects. It features a durable coating on one face for improved performance during the construction phase of projects.
“We have tested SMARTPLY SURE STEP to an aggressive exposure test to ascertain its robustness and understand how it would change dimensionally and on the surface. SMARTPLY MAX (OSB/3), which is the base product that makes up SURE STEP, is a resilient product in its own right. However, when we added on the protective top coat, it brought the dependability of the product to a new level and resulted in us successfully testing the panel to 42 day exposure,” explained Jason.
“I mentioned it to the merchant, who passed the information on, and eventually I had a meeting with Broomhall and Bradshaw to talk through the product and how it would resolve the issue.
“I am pleased to say, it has been a roaring success from that point on. There is no shrinkage now any of the properties completed with SMARTPLY SURE STEP, so it definitely came good on its promise!”
The unique and innovative coating, applied in house at the SMARTPLY factory in Waterford, Ireland, is designed to sustain the effects of the weather and construction foot traffic while reducing the slip risk even in wet conditions.
Phase 2 was completed with SMARTPLY SURE STEP in place of the original product, while phase 3 will be started and completed using SMARTPLY SURE STEP.
Each panel measures 2397 x 1200mm, and comes in thicknesses of 18mm and 22mm. About 50m3 was used, which is approximately 22 packs, to finish phase 2 of the development. They were all supplied by Chadwicks, as will the next orders for phase 3.
“Working with SMARTPLY SURE STEP has been great,” said carpenter Derek Bradshaw, who installed the floors. “You can tell immediately that it is a quality product.
“It’s been around 6 months now since we started using SURE STEP on this project and we’ve had no complaints from occupiers of any floor issues like there were before. With the previous product, it was around 4 months after installation that occupiers started noticing changes, so we’re feeling confident now!”
“I have been back to the site twice after my initial meeting to check on progress, answer any questions and support with technical advice. Everyone involved in the project has been a delight to work with,” Jason concluded.